2.2.3艇體真空導(dǎo)入成型充模過程數(shù)學(xué)模型的建立
由于真空導(dǎo)入成型對RTM成型的繼承性,本文在RTM充模過程數(shù)值模擬的基礎(chǔ)上,對艇體真空導(dǎo)入成型的充模過程進(jìn)行分析。
真空導(dǎo)入成型的關(guān)鍵是通過分配系統(tǒng)使樹脂在表層快速流動(dòng),并在厚度方向緩慢浸潤。同時(shí),由于艇體厚度非常小,樹脂在導(dǎo)流布上的流動(dòng)距離遠(yuǎn)遠(yuǎn)大于在厚度方向上的流動(dòng)距離。由此可知,真空導(dǎo)入成型的充模過程主要取決于導(dǎo)流介質(zhì)的平面滲透率及預(yù)成型體厚度方向的滲透率,而預(yù)成型體的平面滲透率并不屬于關(guān)鍵因素。在上述分析的基礎(chǔ)上,可以假設(shè)預(yù)成型體的浸潤完全是通過樹脂在厚度方向的流動(dòng)完成的,忽略樹脂在預(yù)成型體平面方向的流動(dòng)。由此,可以將艇體真空導(dǎo)入成型的充模過程分為兩個(gè)部分:第一是樹脂在導(dǎo)流布平面方向的流動(dòng),可視為RTM成型工藝中樹脂在二維薄板內(nèi)的流動(dòng);第二部分是樹脂在厚度方向由高滲透介質(zhì)向預(yù)成型體滲流,預(yù)成型體吸收了從導(dǎo)流布滲漏出的樹脂,其流動(dòng)示意圖如圖2-6所示。由此,建立了艇體真空導(dǎo)入成型充模過程的滲漏模型。
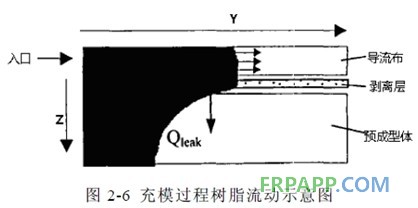
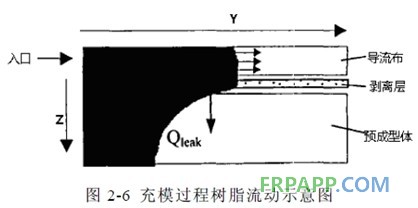
對于RTM二維流動(dòng)的研究大多是基于流體在多孔介質(zhì)中流動(dòng)的達(dá)西定律進(jìn)行的[33-38],其充模過程的二維等溫?cái)?shù)學(xué)模型如下:


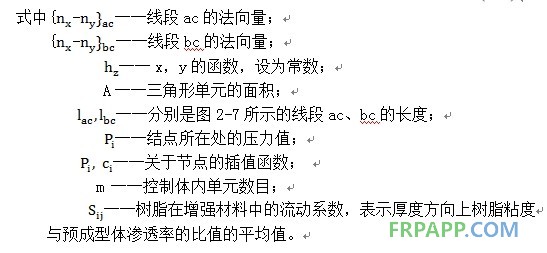
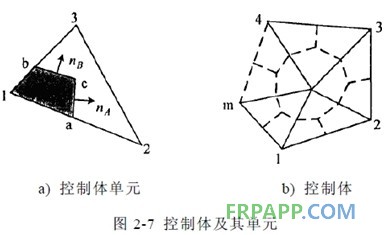
通過上述分析,在式(2-1)中加入Qleak項(xiàng),則滲漏模型的控制方程可寫為:
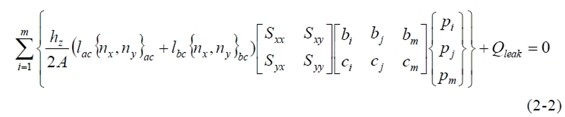
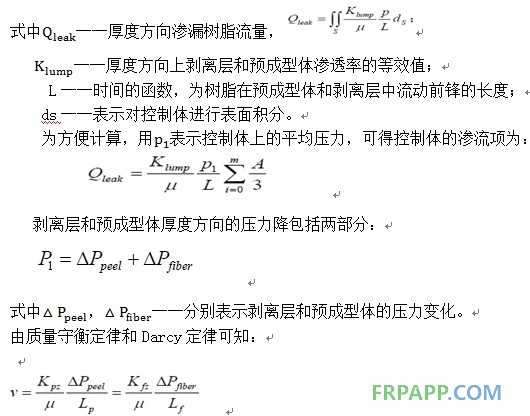
式中 Lp一一預(yù)成型體中樹脂橫向流動(dòng)前峰長度;
Lp----剝離層介質(zhì)的厚度。
由此可得表面速度y如下:
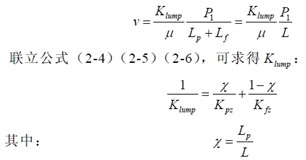
2.3工藝參數(shù)對艇體真空導(dǎo)入成型的影響及材料選擇原則
復(fù)合材料制件成型的顯著特點(diǎn)是材料與結(jié)構(gòu)同時(shí)一體成型,因此,艇體成型中任何一處缺陷都有可能導(dǎo)致整個(gè)艇體的報(bào)廢,造成難以彌補(bǔ)的損失。針對實(shí)際生產(chǎn)中容易出現(xiàn)的缺陷,結(jié)合其成型原理分析各個(gè)工藝參數(shù)對成型質(zhì)量的影響尤為關(guān)鍵[39]。本節(jié)從滲透率、樹脂特性、真空度以及澆注系統(tǒng)的設(shè)計(jì)這幾個(gè)方面進(jìn)行分析[40-42],得出成型材料的選擇原則,以更好的完善工藝設(shè)計(jì)。
2.3.1工藝參數(shù)影響分析
1.滲透率
滲透率是表征樹脂在壓力梯度下通過增強(qiáng)材料時(shí)流動(dòng)的難易程度的物理量。在艇體真空導(dǎo)入成型過程中,由于艇體尺寸大,僅僅依靠外界大氣壓力與模腔內(nèi)真空之間形成的壓力差很難完成填充。因此,通常利用滲透率較高的導(dǎo)流布并鋪設(shè)樹脂管道來促進(jìn)樹脂流動(dòng),完成對整個(gè)模腔的填充。由于導(dǎo)流布滲透率高而增強(qiáng)材料滲透率相對低,充模過程中樹脂在導(dǎo)流布表面迅速流動(dòng),同時(shí)在厚度方向上緩慢浸漬增強(qiáng)材料??梢酝ㄟ^改變導(dǎo)流布使用比例來控制增強(qiáng)材料預(yù)成型體上下表面樹脂流動(dòng)前鋒的距離。鋪層時(shí),剎車區(qū)域的設(shè)置正是利用了這個(gè)特點(diǎn)。
2.樹脂粘度
樹脂流動(dòng)是樹脂在預(yù)成型體中傳遞、運(yùn)輸?shù)那疤岷捅WC。通常情況下,
將材脂在增強(qiáng)材料中的流動(dòng)看做是不可壓縮黏性流體在多孔介質(zhì)中的流動(dòng),其流動(dòng)狀態(tài)可由Darcy定律來描述,如下: