復(fù)合材料是一種具有高強度、高剛性以及具有良好的抗疲勞性、抗腐蝕性等一系列優(yōu)點的新型材料, 已經(jīng)廣泛應(yīng)用于航空航天企業(yè)。在國內(nèi)飛機制造業(yè)中, 復(fù)合材料構(gòu)件的設(shè)計制造大多仍沿用傳統(tǒng)的模擬量尺寸傳遞體系。隨著計算機技術(shù)的發(fā)展,數(shù)字化設(shè)計技術(shù)在飛機制造領(lǐng)域備受關(guān)注, 國內(nèi)航空企業(yè)雖然對利用數(shù)字化技術(shù)實現(xiàn)“無紙化”生產(chǎn)進行了相應(yīng)的摸索和實踐 , 但與國外相比還存在一定的差距, 美國波音公司在波音777 型飛機型號研制中采用數(shù)字化技術(shù), 使研制周期縮短50%, 出錯返工率減少75%, 成本降低25%, 已經(jīng)成為數(shù)字化設(shè)計制造技術(shù)在飛機研制中應(yīng)用的標志和里程碑。
模具是復(fù)合材料構(gòu)件制造用的主要工藝裝備,用以確定制件形狀、結(jié)構(gòu)關(guān)系、控制外緣和獲得良好的表面質(zhì)量, 在模具上完成復(fù)合材料聚合固化,有時還在成形模上進行預(yù)浸料的鋪疊, 復(fù)合材料模具的設(shè)計制造對復(fù)合材料構(gòu)件的產(chǎn)品質(zhì)量影響較大, 要求模具的設(shè)計合理 。國內(nèi)外學(xué)者對普通的機械零件成型模具CAD/ CAM 技術(shù)進行了深入的研究 , 而未見對復(fù)合材料構(gòu)件成型模具的CAD/CAM 技術(shù)的研究。復(fù)合材料構(gòu)件成型模具根據(jù)其材料可分為金屬模和復(fù)合材料模, 因其特殊的結(jié)構(gòu)及工藝, 本文結(jié)合企業(yè)的實際需求, 以典型的復(fù)合材料構(gòu)件成型模具結(jié)構(gòu)為研究對象, 研究了現(xiàn)有模具設(shè)計過程中存在的問題, 提出了改進的設(shè)計方法, 將復(fù)合材料構(gòu)件成型模具設(shè)計分為3 個階段進行: 成型曲面的檢測, 模具體的設(shè)計, 模具支架的參數(shù)化設(shè)計, 并開發(fā)了相應(yīng)的設(shè)計系統(tǒng)。
1 典型復(fù)合材料構(gòu)件模具結(jié)構(gòu)分析
復(fù)合材料構(gòu)件成型模具的結(jié)構(gòu)隨著工藝方法的變化而變化, 比較有代表性的是真空袋( 熱壓灌成形方法的模具) , 如圖1 所示為薄板框架式模具的結(jié)構(gòu)示意圖, 包括用于鋪帖復(fù)合材料成型模具的過渡模, 其結(jié)構(gòu)設(shè)計包含的基本內(nèi)容有以下幾個方面: 模具型面要具有較高的精度, 這是復(fù)合材料構(gòu)件成型的基本依據(jù); 如果模具體是金屬模, 其型面需采用數(shù)控加工, 在設(shè)計過程中應(yīng)滿足加工的具體要求, 如果是用復(fù)合材料( 通常使用纖維增強樹脂)來做模具體, 在國內(nèi)大都采用人工鋪帖成型的方式
進行制造, 型板架大都是金屬管材或角材組成的框架, 其通過數(shù)控加工的方式制造的, 在設(shè)計過程中要考慮到鋪帖成型的模具體要在允許的誤差范圍內(nèi), 才能保證成型模具體與型板架成功裝配, 保證模具體的精度。此外, 型架板結(jié)構(gòu)主要考慮保證在加溫時模具體不易變形, 而且使得空氣流在模具體上下表面任意流動。
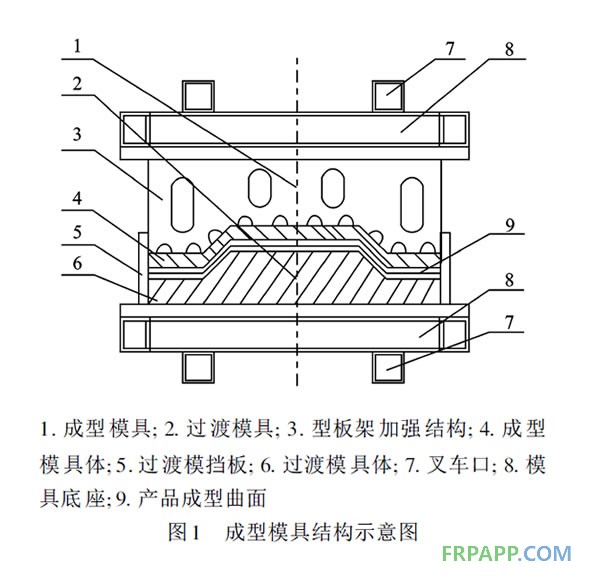
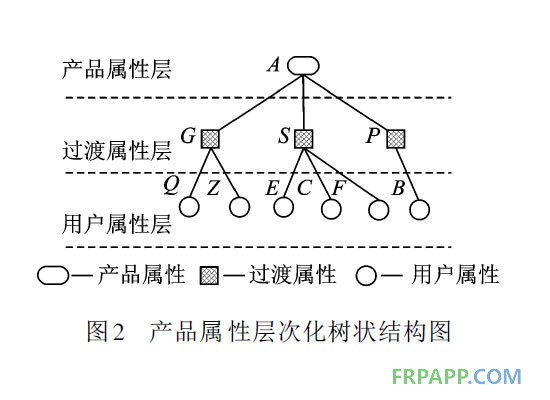
模具是復(fù)合材料構(gòu)件制造用的主要工藝裝備,用以確定制件形狀、結(jié)構(gòu)關(guān)系、控制外緣和獲得良好的表面質(zhì)量, 在模具上完成復(fù)合材料聚合固化,有時還在成形模上進行預(yù)浸料的鋪疊, 復(fù)合材料模具的設(shè)計制造對復(fù)合材料構(gòu)件的產(chǎn)品質(zhì)量影響較大, 要求模具的設(shè)計合理 。國內(nèi)外學(xué)者對普通的機械零件成型模具CAD/ CAM 技術(shù)進行了深入的研究 , 而未見對復(fù)合材料構(gòu)件成型模具的CAD/CAM 技術(shù)的研究。復(fù)合材料構(gòu)件成型模具根據(jù)其材料可分為金屬模和復(fù)合材料模, 因其特殊的結(jié)構(gòu)及工藝, 本文結(jié)合企業(yè)的實際需求, 以典型的復(fù)合材料構(gòu)件成型模具結(jié)構(gòu)為研究對象, 研究了現(xiàn)有模具設(shè)計過程中存在的問題, 提出了改進的設(shè)計方法, 將復(fù)合材料構(gòu)件成型模具設(shè)計分為3 個階段進行: 成型曲面的檢測, 模具體的設(shè)計, 模具支架的參數(shù)化設(shè)計, 并開發(fā)了相應(yīng)的設(shè)計系統(tǒng)。
1 典型復(fù)合材料構(gòu)件模具結(jié)構(gòu)分析
復(fù)合材料構(gòu)件成型模具的結(jié)構(gòu)隨著工藝方法的變化而變化, 比較有代表性的是真空袋( 熱壓灌成形方法的模具) , 如圖1 所示為薄板框架式模具的結(jié)構(gòu)示意圖, 包括用于鋪帖復(fù)合材料成型模具的過渡模, 其結(jié)構(gòu)設(shè)計包含的基本內(nèi)容有以下幾個方面: 模具型面要具有較高的精度, 這是復(fù)合材料構(gòu)件成型的基本依據(jù); 如果模具體是金屬模, 其型面需采用數(shù)控加工, 在設(shè)計過程中應(yīng)滿足加工的具體要求, 如果是用復(fù)合材料( 通常使用纖維增強樹脂)來做模具體, 在國內(nèi)大都采用人工鋪帖成型的方式
進行制造, 型板架大都是金屬管材或角材組成的框架, 其通過數(shù)控加工的方式制造的, 在設(shè)計過程中要考慮到鋪帖成型的模具體要在允許的誤差范圍內(nèi), 才能保證成型模具體與型板架成功裝配, 保證模具體的精度。此外, 型架板結(jié)構(gòu)主要考慮保證在加溫時模具體不易變形, 而且使得空氣流在模具體上下表面任意流動。
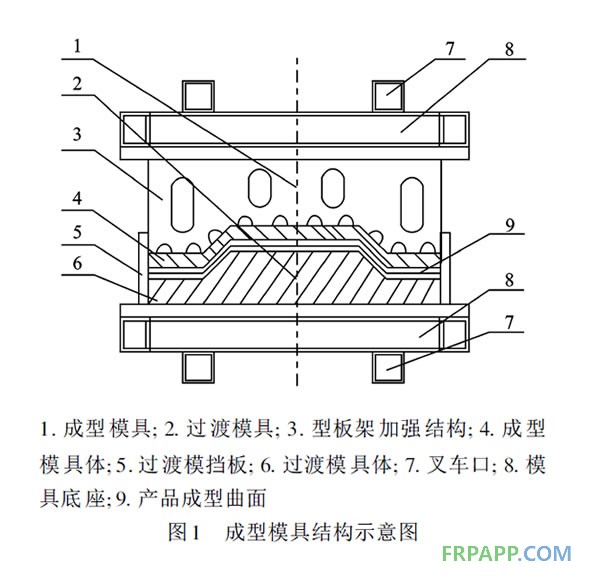
2 現(xiàn)有設(shè)計存在的問題
在以數(shù)字量傳遞的設(shè)計中, 復(fù)合材料構(gòu)件模具的設(shè)計原始依據(jù)是飛機構(gòu)件的外形曲面, 模具的設(shè)計過程受上游數(shù)據(jù)的影響較大。現(xiàn)有的設(shè)計中, 設(shè)計者沒有對上游曲面數(shù)據(jù)進行客觀的評價, 往往只有在制造的過程中才能發(fā)現(xiàn)產(chǎn)品數(shù)據(jù)的不足, 出現(xiàn)加工迭代的現(xiàn)象, 造成資源浪費。本文結(jié)合并行工程及可制造性的設(shè)計思想, 在設(shè)計階段能根據(jù)現(xiàn)有的資源條件等, 對接收的產(chǎn)品曲面數(shù)據(jù)進行綜合評價, 輔助設(shè)計者合理地作出判斷, 對產(chǎn)品數(shù)據(jù)的不足及時地進行修改, 滿足要求。
復(fù)合材料構(gòu)件模具體設(shè)計的主要工作是對成型曲面的偏置, 成型曲面是大量的曲面片拼接而成的, 其特征非常復(fù)雜, 在對復(fù)合材料構(gòu)件模具體設(shè)計過程中, 對成型曲面進行偏置時, 存在局部因曲率過大而無法整體偏置的問題, 使得設(shè)計人員不得不將原始曲面進行拆分, 而分別對曲面片進行單獨偏置, 然后將所得的偏置曲面按要求進行拼接。這樣不僅改變了原始的設(shè)計數(shù)據(jù), 使得設(shè)計結(jié)果有較大的偏差, 往往需要設(shè)計員進行無數(shù)次的反復(fù)嘗試, 才能得到合理的解, 而且對曲面的處理, 本身就是很復(fù)雜的過程, 依靠人工的手段, 質(zhì)量得不到保證, 而且降低了設(shè)計效率。本文在滿足誤差的前提下, 提出了基于誤差約束的復(fù)雜曲面整體偏置方法。
型架板結(jié)構(gòu)的設(shè)計過程中, 設(shè)計者對每一個結(jié)構(gòu)的設(shè)計都從草圖進行, 設(shè)計步驟煩瑣, 設(shè)計效率低下, 依賴設(shè)計人員所掌握的知識和經(jīng)驗, 不同背景的設(shè)計人員所設(shè)計的產(chǎn)品模型差異很大, 不能滿足產(chǎn)品規(guī)范性的要求。通過對大量復(fù)合材料構(gòu)件模具的總結(jié), 發(fā)現(xiàn)其型架板結(jié)構(gòu)大同小異, 本文利用參數(shù)化設(shè)計手段對其進行標準化, 建立其參數(shù)化設(shè)計模型, 設(shè)計者只需對給定的幾組參數(shù)進行賦值,便可以生成滿足條件的型架板結(jié)構(gòu), 減少設(shè)計者的大量而煩瑣的重復(fù)繪圖工作, 提高設(shè)計效率。
3 成型曲面的檢測方法
復(fù)合材料構(gòu)件因其特殊的結(jié)構(gòu), 其成型表面是通過大量的曲面片拼接而成的, 表面質(zhì)量較差, 因此進行模具設(shè)計, 特別是以數(shù)控加工方式加工的產(chǎn)品時, 必須要對成型面進行可加工性檢測, 判斷成型面在企業(yè)現(xiàn)有的加工資源條件下能否高效加工出合格的產(chǎn)品。本文考慮影響成型面可制造性的因素包括: 加工難度、加工設(shè)備、刀具、裝夾方式等, 并將這些因素映射為成型面的幾何特征屬性, 使設(shè)計者在設(shè)計過程中能根據(jù)幾何特征合理判斷其可加工性。作者在文獻[ 6] 中詳細論述了成型曲面的檢測方法, 本文簡述如下。
3. 1 成型曲面幾何特征屬性的提取
影響模具可加工性的屬性可分為產(chǎn)品屬性層、過渡屬性層和用戶屬性層。產(chǎn)品屬性層指影響其可加工性的總體屬性, 用A 表示。過渡屬性層指由產(chǎn)品屬性向用戶屬性過渡的中間屬性集合, 其可分為成型曲面的幾何形狀屬性G, 現(xiàn)有的制造資源屬性S 以及模具幾何屬性P。根據(jù)成型曲面特征對加工工藝性的影響的不同, 將成型曲面的幾何形狀屬性可進一步分為局部特征屬性Q( 如曲面上某點的曲率、曲面的凹凸性等) , 和整體特征屬性Z ( 如曲面是否為單值曲面等) 。制造資源屬性可進一步分為加工設(shè)備屬性E , 刀具屬性C, 裝夾屬性F 等。模具的幾何屬性主要是指模具幾何特征對成型曲面的加工工藝性產(chǎn)生影響的屬性, 如在數(shù)控加工, 是否以模具上的某特征作為加工成型曲面的定位基準, 將會影響成型曲面的加工工藝性。本文主要考慮在設(shè)計模具時, 將加工成型曲面的裝夾定位的基準設(shè)計為模具的局部特征, 即將設(shè)計基準和定位基準定義為同一基準, 簡化模具的設(shè)計步驟和裝夾的工藝, 稱為模具的基準屬性B。它們之間的層次映射關(guān)系為A = {G , S , P } = {Q, Z, E, C, F, B} , 各屬性的層次化樹狀結(jié)構(gòu)如圖2 所示, 用戶最終只需關(guān)注用戶屬性層的屬性, 簡化后續(xù)的設(shè)計與計算。
在以數(shù)字量傳遞的設(shè)計中, 復(fù)合材料構(gòu)件模具的設(shè)計原始依據(jù)是飛機構(gòu)件的外形曲面, 模具的設(shè)計過程受上游數(shù)據(jù)的影響較大。現(xiàn)有的設(shè)計中, 設(shè)計者沒有對上游曲面數(shù)據(jù)進行客觀的評價, 往往只有在制造的過程中才能發(fā)現(xiàn)產(chǎn)品數(shù)據(jù)的不足, 出現(xiàn)加工迭代的現(xiàn)象, 造成資源浪費。本文結(jié)合并行工程及可制造性的設(shè)計思想, 在設(shè)計階段能根據(jù)現(xiàn)有的資源條件等, 對接收的產(chǎn)品曲面數(shù)據(jù)進行綜合評價, 輔助設(shè)計者合理地作出判斷, 對產(chǎn)品數(shù)據(jù)的不足及時地進行修改, 滿足要求。
復(fù)合材料構(gòu)件模具體設(shè)計的主要工作是對成型曲面的偏置, 成型曲面是大量的曲面片拼接而成的, 其特征非常復(fù)雜, 在對復(fù)合材料構(gòu)件模具體設(shè)計過程中, 對成型曲面進行偏置時, 存在局部因曲率過大而無法整體偏置的問題, 使得設(shè)計人員不得不將原始曲面進行拆分, 而分別對曲面片進行單獨偏置, 然后將所得的偏置曲面按要求進行拼接。這樣不僅改變了原始的設(shè)計數(shù)據(jù), 使得設(shè)計結(jié)果有較大的偏差, 往往需要設(shè)計員進行無數(shù)次的反復(fù)嘗試, 才能得到合理的解, 而且對曲面的處理, 本身就是很復(fù)雜的過程, 依靠人工的手段, 質(zhì)量得不到保證, 而且降低了設(shè)計效率。本文在滿足誤差的前提下, 提出了基于誤差約束的復(fù)雜曲面整體偏置方法。
型架板結(jié)構(gòu)的設(shè)計過程中, 設(shè)計者對每一個結(jié)構(gòu)的設(shè)計都從草圖進行, 設(shè)計步驟煩瑣, 設(shè)計效率低下, 依賴設(shè)計人員所掌握的知識和經(jīng)驗, 不同背景的設(shè)計人員所設(shè)計的產(chǎn)品模型差異很大, 不能滿足產(chǎn)品規(guī)范性的要求。通過對大量復(fù)合材料構(gòu)件模具的總結(jié), 發(fā)現(xiàn)其型架板結(jié)構(gòu)大同小異, 本文利用參數(shù)化設(shè)計手段對其進行標準化, 建立其參數(shù)化設(shè)計模型, 設(shè)計者只需對給定的幾組參數(shù)進行賦值,便可以生成滿足條件的型架板結(jié)構(gòu), 減少設(shè)計者的大量而煩瑣的重復(fù)繪圖工作, 提高設(shè)計效率。
3 成型曲面的檢測方法
復(fù)合材料構(gòu)件因其特殊的結(jié)構(gòu), 其成型表面是通過大量的曲面片拼接而成的, 表面質(zhì)量較差, 因此進行模具設(shè)計, 特別是以數(shù)控加工方式加工的產(chǎn)品時, 必須要對成型面進行可加工性檢測, 判斷成型面在企業(yè)現(xiàn)有的加工資源條件下能否高效加工出合格的產(chǎn)品。本文考慮影響成型面可制造性的因素包括: 加工難度、加工設(shè)備、刀具、裝夾方式等, 并將這些因素映射為成型面的幾何特征屬性, 使設(shè)計者在設(shè)計過程中能根據(jù)幾何特征合理判斷其可加工性。作者在文獻[ 6] 中詳細論述了成型曲面的檢測方法, 本文簡述如下。
3. 1 成型曲面幾何特征屬性的提取
影響模具可加工性的屬性可分為產(chǎn)品屬性層、過渡屬性層和用戶屬性層。產(chǎn)品屬性層指影響其可加工性的總體屬性, 用A 表示。過渡屬性層指由產(chǎn)品屬性向用戶屬性過渡的中間屬性集合, 其可分為成型曲面的幾何形狀屬性G, 現(xiàn)有的制造資源屬性S 以及模具幾何屬性P。根據(jù)成型曲面特征對加工工藝性的影響的不同, 將成型曲面的幾何形狀屬性可進一步分為局部特征屬性Q( 如曲面上某點的曲率、曲面的凹凸性等) , 和整體特征屬性Z ( 如曲面是否為單值曲面等) 。制造資源屬性可進一步分為加工設(shè)備屬性E , 刀具屬性C, 裝夾屬性F 等。模具的幾何屬性主要是指模具幾何特征對成型曲面的加工工藝性產(chǎn)生影響的屬性, 如在數(shù)控加工, 是否以模具上的某特征作為加工成型曲面的定位基準, 將會影響成型曲面的加工工藝性。本文主要考慮在設(shè)計模具時, 將加工成型曲面的裝夾定位的基準設(shè)計為模具的局部特征, 即將設(shè)計基準和定位基準定義為同一基準, 簡化模具的設(shè)計步驟和裝夾的工藝, 稱為模具的基準屬性B。它們之間的層次映射關(guān)系為A = {G , S , P } = {Q, Z, E, C, F, B} , 各屬性的層次化樹狀結(jié)構(gòu)如圖2 所示, 用戶最終只需關(guān)注用戶屬性層的屬性, 簡化后續(xù)的設(shè)計與計算。
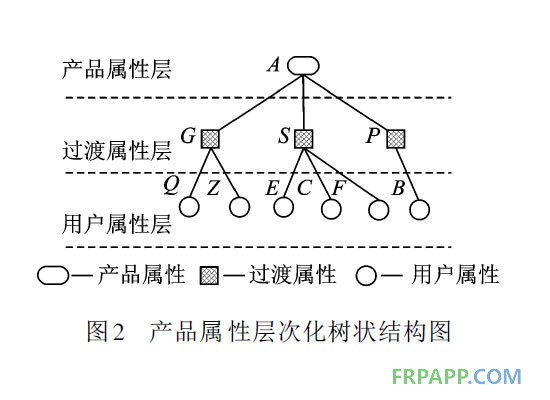